Moisture penetration into concrete structures can lead to cracking, spalling, efflorescence (white crystalline salt deposits), and other forms of deterioration if left unchecked. Waterproofing prevents damage and saves on maintenance costs and repairs.
Using the latest crystalline waterproofing technologies, concrete can be protected from water damage and other environmental hazards. Here are the key benefits of Waterproof Concrete Staten Island:
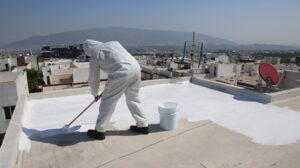
Prevents Mold And Mildew
Mold and mildew are a serious issue that affects the aesthetics of any structure and can pose health risks for anyone who inhabits a building or home. It is essential to prevent the growth of these microbes by establishing a strong barrier against moisture in construction projects. Waterproof concrete can accomplish this task, while also strengthening the integrity of any foundation or structure. Waterproof concrete is a great option for basements, foundations, maintaining partitions, and other locations that are prone to humidity.
Mold thrives in damp areas that supply a stable food source. This fungus commonly grows in dirt, dust, pollen, bacteria, and other organic materials. In nature, mold is beneficial to the environment, as it deteriorates dead material and makes room for new plant and animal life. However, this natural phenomenon can cause severe problems in structures when it reaches unacceptable levels.
When mold forms in concrete, it often requires extensive remediation efforts to remove the spores and their surrounding staining. These methods may include scrubbing, etching, or blasting. In addition, a fungicide can be used to deactivate and kill the mold spores. However, this will not eliminate the stains and discoloration caused by the mold and can result in the spread of the spores to other areas of the building or home.
Waterproof concrete creates a sturdy barrier that prevents the infiltration of moisture into a structure. This prevents the damaging effects of moisture, such as spalling, cracking, and corrosion of steel reinforcement. It is an excellent choice for basements, foundations, and other areas that are prone to moisture in construction projects.
In addition to its ability to withstand the harsh effects of moisture, waterproof concrete is stronger and more durable than traditional concrete. This enhanced strength and durability will help to reduce maintenance costs and improve the overall structural integrity of the construction project. It will also provide significant energy efficiency benefits by reducing the need for constant heating and cooling in buildings. These advantages will ultimately result in reduced energy bills and a greater return on investment for the owner.
Prevents Leaks
Concrete is a very durable building material, but it’s also highly porous. Moisture penetration can cause a range of problems, including surface cracking, spalling, corrosion of steel reinforcing bars, efflorescence (white powdery deposits on the surface), and the growth of mold or mildew. Waterproofing prevents these issues by creating a barrier that protects concrete from water penetration.
While there are some ways to reduce the amount of cracking that occurs in concrete, such as using certain admixtures during the mixing process, even the most perfectly mixed concrete will eventually develop cracks over time. These cracks can then allow water to seep into the concrete, which can result in damage and deterioration over time. Waterproof concrete is more resilient and can withstand the forces of nature without cracking, resulting in less maintenance and repair costs down the road.
When a crack in concrete appears, it is important to address the problem right away. One of the best ways to do this is by caulking expansion joints and any existing cracks in the concrete. Waterproof concrete caulk is a great choice because it can be applied to any size of crack and will seal the concrete to prevent moisture from entering through these cracks.
Adding waterproof concrete to your project can also help with energy efficiency. The fact that it keeps water out enables the structure to hold a steady temperature and reduces the need for constant heating and cooling, which in turn results in lower energy bills over time.
Whether you are building a new residential driveway, a concrete slab for an elevated garden, or a commercial parking garage, waterproof concrete solutions are a smart investment. Not only does it save on long-term repairs and maintenance, but it also adds to the value of your property. For more information about the different concrete waterproofing solutions that are available, speak with an expert today. They can provide you with a free quote and tailored advice about the best solution for your property. Alternatively, you can contact us online to get started. We look forward to hearing from you soon!
Prevents Damage
Whether you’re looking to protect your new foundation, basement, or concrete slab in a commercial building, or simply your home, a waterproof concrete solution can make all the difference. This game-changing innovation prevents the damaging effects of moisture infiltration, extending the life of your structure and saving you money.
Moisture is one of the most destructive forces in the world, causing concrete to deteriorate over time. Concrete structures that are exposed to water damage experience several problems including cracking, spalling, and corroding. This deterioration can lead to the breakdown of the concrete itself, exposing matrix materials and base concrete. In addition to reducing the structural integrity of the building, this can also affect the appearance of the concrete, resulting in costly repairs and replacements.
Waterproof concrete solutions are designed to combat these issues by preventing moisture infiltration and promoting proper curing. By effectively managing surface water, it reduces the risk of flooding and freezing temperatures by allowing excess water to drain away quickly. It also improves the concrete’s water-cement ratio and allows it to dry more quickly, minimizing any potential damage that can occur from freezing and thawing.
By keeping mold and mildew from developing, waterproof concrete solutions also help to maintain a healthy environment inside your building. This is because mold and mildew can be harmful to human health, causing respiratory problems and lowering air quality in your building. Waterproof concrete creates a strong moisture barrier, helping to keep mold and mildew at bay and ensuring that your building has a clean, fresh look.
Waterproof concrete also helps to improve energy efficiency by regulating temperature and preventing energy loss. It acts as a barrier against moisture, reducing the strain on heating and cooling systems and lowering energy bills over time. In addition, it prevents the buildup of dirt and ice around the foundation, making cleaning and maintenance much easier.
Increases Property Value
Waterproof concrete is a valuable addition to the construction process, providing long-term benefits that increase the value of a structure. These benefits include extended longevity and structural integrity, protection against moisture-related issues such as mold and mildew, and reduced maintenance costs.
Concrete is made of a combination of cement, aggregate, and sand. During the mixing and curing process, water is used to activate chemical reactions and form the hard, durable material. Despite its strength and durability, concrete is porous by nature. The ability of concrete to absorb water, and moisture in particular, is a significant issue when building or maintaining concrete structures.
When the proper waterproofing admixture is added to concrete during the mixing process, it creates a barrier that prevents moisture from entering the concrete. It’s important to note that this method of waterproofing isn’t designed to replace regular concrete or mortar, but it is a useful alternative in situations where the concrete will be exposed to extreme moisture and hydrostatic pressure.
The key to waterproofing is a high-quality admixture that reduces the permeability of concrete, preventing moisture from passing through and damaging the concrete. During the curing process, it’s also imperative to monitor and control the rate of water evaporation to ensure the concrete isn’t over-saturated.
Moisture in concrete causes a wide range of problems, including the formation of cracks, corrosion of steel reinforcement, efflorescence (white or gray deposits on the surface), and mold and mildew growth. Repairing damage caused by moisture is expensive and invasive, and can often lead to structural issues that require replacement of the entire concrete structure. Waterproofing concrete during construction can prevent these issues from occurring and protect the structure for its lifetime.
Although waterproofing a concrete structure requires an additional cost, it’s worth the investment. It’s more affordable and streamlined than repairing a damaged concrete foundation or wall later on and can save you the expense of replacing your property. It also adds to the overall value of your home or business, giving future buyers peace of mind that they’re investing in a safe, secure, and long-lasting structure.