Your fence is a critical part of your property, providing security & privacy. It is also a visual enhancement that can add to the value of your home.
Regular inspections are key to identifying issues early, whether they are rust on metal fences or loose boards on wooden ones. These problems can easily escalate if left unchecked. Better talk with Charlotte Fence Contractor to maintain your fence.
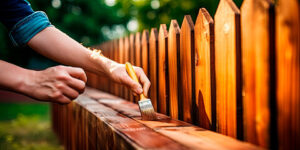
Inspect The Fence Regularly
A shabby-looking fence can pull the look of your entire yard down, so it’s important to make regular inspections and address any issues that arise. You can start by walking the length of your fence and checking for loose boards or sagging sections. If you see any problems, take note of them and get them fixed right away to prevent them from worsening.
You should also check for rotted or weakened boards, and tighten any loose nails or screws. These small repairs can help extend the life of your fence, so it’s important to catch them early on before they cause more damage or become a safety hazard for people passing by.
It’s also a good idea to inspect the fence for signs of weather damage. For example, wood may deteriorate more quickly when it’s exposed to constant moisture, so you should regularly wash your fence with a hose to prevent mold and other issues from developing. Additionally, metal components may rust if they’re not protected with weatherproofing treatment, so you should periodically sand and apply a coat of protective paint or stain.
You should also regularly clean your fence to remove debris, like leaves, branches, and trash. This can help keep your fence looking great and ensure that it’s free of any weeds or other plants that could damage it over time. In addition, you should trim any vegetation that’s growing near your fence, as this can block the sunlight and contribute to rot or other problems. Lastly, you should regularly clean your gate hardware and secure it to ensure proper functionality and safety.
Clean The Fence Regularly
Cleaning your fence regularly prevents it from getting dirty and helps extend its lifespan. Dirt, mildew, and moss buildup can be corrosive and contribute to material breakdown. Hosing your fence down with a garden hose or cleaning solution formulated for your specific material can remove these and leave your fence looking new. If your fence is made of wood, it’s a good idea to scrub it with a long-handled brush or power washer (at a low psi setting) once or twice a year. For pressure washing, be sure to work in small sections to avoid splintering the wood.
After scrubbing or pressure-washing, be sure to let the fence dry before applying any sealants or paint. A wood stain or sealer is a protective coating that preserves your fence from moisture, sun damage, and pest infestation. For a beautiful appearance, choose a tinted stain that highlights the natural grain of the wood. Depending on your climate, a wood stain may need to be reapplied every three years or so.
Brick and metal fencing require less maintenance but should be inspected for loose or damaged panels, posts, or bolts. Detecting these issues early lets you make repairs promptly to prolong the life of your fence. Regular inspections can also help you spot problems like wood rot or insect infestation before they get out of hand.
Other steps that will help you maintain the quality and beauty of your fence include minimizing water intrusion, which can cause wood to rot or lead to the growth of moss. Adjust your sprinklers so that the fence doesn’t get wet or soak in standing water, and trim vegetation close to the wall to keep plants from hanging over it.
Apply Stain Or Paint
Keeping your fence stained or painted provides another layer of protection from moisture and UV damage. It also helps to keep the wood from warping and cracking. Typically, you can expect a stain to last two to five years before it needs to be reapplied. The frequency of reapplying depends on your climate conditions and the type of stain you choose.
Stains can be applied using a brush, roller, or sprayer. Before staining, ensure the surface is clean of debris and dirt. If the stain is old and worn, a coat of wood brightener may be needed to help restore its original color and protect the wood.
Before applying any stain, always read the product label, technical data sheet (TDS), and safety data sheet for application instructions. Be sure to test the stain on a small, hidden area of your fence to make certain you are happy with the color and to ensure it will adhere properly.
When choosing a stain, consider whether you want it opaque or transparent. Both will protect from weather and the sun, but opaque stains provide a more dramatic effect while semitransparent stains allow you to see the natural grain of the wood.
If you are unsure whether your fence is due for a new coat of stain, try the splash test: sprinkle water on a section of the wood. If it absorbs within five seconds, the wood needs to be treated.
If you choose to repaint, be sure to wear a pair of chemical-resistant gloves and a face mask. If you are sensitive to volatile organic compounds (VOCs), it’s a good idea to wear a respirator as well. It is also important to protect the plants, furniture, and grills near your fence with plastic drop cloths.
Repair Broken Or Loose Hardware
If you have a wood fence, it’s essential to regularly inspect and repair any sections that are damaged or in need of repairs. This can include loose boards or sections that need to be hammered in or tightened, as well as checking that all screws and nails are secure and a good length from the end of the post. Inspecting the connections between the posts and the panels is particularly important, as these can be damaged by moisture penetration and increase the risk of rot.
A regular clean-up can also help to extend the lifespan of your fence. This includes removing debris such as leaves and other organic material, which can trap moisture and lead to rot and decay. During clean-up, it’s also a good idea to clear away any tree branches that rub against the fence.
Staining or painting your fence can help to prevent rot and protect it from moisture and the sun’s UV rays. Wood preservatives can be applied as a protective coat and should be re-applied every 2-3 years.
In addition to cleaning and staining, you should also make sure that the area around your fence drains well. This will help to prevent water pooling and rotting the posts, and can be done by ensuring that all sprinklers are directed away from the fence and soil is not being saturated.
If you have a metal fence, it’s also important to check that the gate hinges and locks are still in working order and that they’re securely attached and the posts. Loose hinges or locks can cause the gate to become unusable, and the lock may need to be replaced if it’s worn out or damaged.
Trim Overhanging Branches
Living in a neighborhood adorned with lush trees can be a beautiful experience. But the beauty also comes with a responsibility. Trees must be trimmed regularly to ensure that they are not too close to homes, cars, or structures. If left unattended, overhanging branches can pose serious damage to properties. They can smack against roofs, leaving massive dents or even holes, and they can also damage fences by rubbing against them. Additionally, overgrown tree branches can also lead to rot and insect infestations, which can cause more extensive damage to your property.
Keeping trees trimmed can also help with home values and aesthetics. A property that has overgrown branches may look unkempt, and this can turn off potential buyers. However, tackling this issue can be tricky. While a homeowner is generally within their rights to trim or remove branches that are overhanging on their property, it’s important to be aware of state and local laws and regulations. A professional tree trimming service can help ensure that all branches are trimmed legally and appropriately.
It is also important to keep in mind that if you trim or prune a tree that’s on your neighbor’s property and it causes any damage, you could be liable. According to the legal advice website, this can be true even if you are not cutting the entire tree. In this case, it is best to work with your neighbors on a mutually agreed upon time to trim the trees that are overhanging each other’s property.
When a tree branch is overhanging your property, you should always cut the branch just outside of the bark ridge (it’s easier to see on some types of trees than others). This allows the wound to heal properly and avoids damaging the collar.